What is planned maintenance?
Planned maintenance applies to maintenance activities that are scheduled, planned in advance, or even designed. It is a proactive maintenance approach to building and equipment upkeep.
It involves regular inspections, maintenance activities, and preventive maintenance tasks. The goal is to identify and fix potential problems before they occur.
Planned maintenance is also an excellent opportunity to check for code updates and ensure that your building is up to date. It typically happens on a regular schedule, such as monthly, quarterly, or yearly.
But the frequency can be adjusted based on the needs of your property.
For example, an office building in a high-traffic area should be checked more often than a retail store that is not as busy.
Planning maintenance is crucial, as maintenance work can be disruptive. You can schedule it for a time that works best for your business and avoid wasting time on repairs that could have been prevented.
Buildings are like people — they need regular check-ups to ensure everything is functioning well.
Just as you would schedule a yearly visit with your doctor, buildings need regular tune-ups to keep them operating at peak efficiency.
And the best way to do that is planned maintenance.
It is key to keeping your property in good condition and ensuring that minor problems don’t turn into big (and expensive) ones.
What does the planned maintenance landscape look like in 2022?
The rise of planned maintenance has been one of the most significant changes in the real estate industry over the past decade.
We also see automation slowly creeping into the sector, with predictive maintenance software becoming more mainstream.
Software and hardware are also starting to get involved following the 4th industrial revolution.
This paper by the University Politehnica of Bucharest, Machine and Manufacturing Systems Department highlights:
The IoT platforms provide good support for predictive maintenance as they can integrate information from different machines and manufacturing systems.
IoT-enabled devices are being used to monitor building performance and maintenance needs in real estate, with the data collected sent back to a central system for analysis.
For example, service robots are used to inspect buildings and send back reports, while drones are used to assess roofing and facade damage.
Another significant change we're seeing is the move towards green buildings and sustainable maintenance practices.
Planned maintenance plays an essential role in this, with more and more landlords and property managers looking to adopt eco-friendly policies.
It's not just about being environmentally responsible; these measures can also save money in the long run.
For example, solar panels can be installed to help power a building, and rainwater harvesting can be used to reduce water consumption.
These are important because they cut your costs, and customers are increasingly interested in sustainable buildings.
As Frans Melissen, Bert Smit, and Vitalija Danivska write in the book "Rethinking Sustainability in Facilities and Workplace Management":
[...]consumers seem to value sustainable products and services more and more. As a result, some consumers are willing to pay more for sustainable products and services than unsustainable alternatives. Of course, this is not true for all consumers. Still, an ever-increasing percentage of consumers favors a sustainable product or service over an unstainable one if the price they have to pay is (somewhat) similar.
So, what does the future of planned maintenance look like?
We're moving towards more automated, data-driven portfolio operations where sustainability is increasingly important. And that can only be a good thing for the industry as a whole.
In the future, we'll see even more buildings using these technologies as part of their planned maintenance regime.
Schedule a call today and learn how Facilio is the best option to carry out your planned maintenance tasks.
Different types of planned maintenance
There are two types of planned maintenance: planned preventive maintenance and unscheduled maintenance.
Let's look at both types:
Planned preventive maintenance
Planned preventive maintenance (PPM) is a regular schedule of routine maintenance tasks.
The goal of PPM is to prevent problems from occurring in the first place or to identify them early so they can be fixed before they cause damage or become expensive to repair.
Typically, PPM is performed on equipment critical to a business's operation, such as HVAC systems, elevators, and boilers.
However, PPM can also be performed on non-critical equipment, such as office furniture and computers. PPM is typically scheduled in advance and carried out regularly, such as weekly, monthly, or quarterly.
A planned maintenance schedule also helps you avoid — or cut — unplanned downtime. For example, imagine your building’s heating, ventilation, and air conditioning (HVAC) system breaking down in the middle of summer.
Without a properly functioning HVAC system, your tenants will be uncomfortable and may even start to look for a new place to live. Unfortunately, that's when your apartments become vacant, which means revenue loss.
Suggested read: How to Build a Preventive Maintenance (PM) Checklist?
Planned unscheduled maintenance
Planned unscheduled maintenance is a legitimate planned maintenance technique that involves delaying the upkeep of an asset until it breaks down.
It might sound contradictory, but this strategy can save money and lives in some industries where critical equipment cannot fail at an inopportune moment.
When you experience equipment problems, your best option is to plan for them before encountering a breakdown.
Planned unscheduled maintenance is appropriate when repairing equipment after a failure exceeds the overall expense of preventing such failures.
Planned unscheduled maintenance fits right in if the asset is:
- Single-use and is inexpensive
- Does not have statutory requirements
- Non-critical
- Low value
- Has a short lifespan
You can also include assets with a low chance of failing whose failure pattern is not random.
Planned maintenance example
A typical planned maintenance program is a yearly tune-up of your building's HVAC system.
This involves checking the system for leaks, cleaning the coils, and checking the wiring. It's an excellent way to ensure that your HVAC system runs smoothly and efficiently.
Another example is cleaning gutters. This is typically done in the fall before the leaves start to accumulate. Keeping the gutters clean can prevent water damage to your roof and foundation.
With planned maintenance, you ensure your critical assets are protected and your equipment runs smoothly and efficiently.
Having your assets in good condition ensures improved workplace management, and you can avoid liabilities and workplace accidents.
A host of benefits come with keeping your buildings and equipment in top shape.
Get in touch with us today and find out how Facilio can help you seamlessly handle planned maintenance.
What are the 4 phases of planned maintenance?
Planned maintenance can be subdivided into four basic categories:
- Predictive maintenance
- Preventive maintenance
- Corrective maintenance
- Risk-based maintenance
These four phases of maintenance—equipment management, building envelope testing and repair/replacement, general repairs and upgrades, and system redundancies—should be used together for the most comprehensive approach to building maintenance.
Predictive maintenance
Predictive maintenance (PdM) uses conditional monitoring to spot signs of damage, oddities, and performance issues using real-time asset data.
Using PdM, you can estimate equipment failure time, why it fails, and how to fix it. As a result, you can be on top of potential issues and line up resources to fix them even before failure.
Preventive maintenance
Preventive maintenance is a method that helps plan routine maintenance activities that aim to boost assets, resources, and buildings.
Predictive maintenance also helps reduce the possibility of unforeseen equipment faults and unplanned downtime and helps prevent resorting to reactive maintenance.
Corrective maintenance
Corrective maintenance is an approach that helps fix the problem after it occurs. It's a reactive way of maintenance, and it is generally preferred to be used for assets that are not very expensive and those that do not significantly impact business.
Risk-based maintenance
This maintenance phase involves identifying the risk of an event occurring—whether for a minor repair or catastrophic failure—and determining what needs to be done based on those risks.
It involves:
- Analyzing data to predict when equipment is likely to fail
- Ranking risks according to their likelihood and impact
- Managing risks by implementing strategies that eliminate unacceptable risks and lessen the effects of manageable ones.
Identifying and analyzing risks and developing plans to address them allows organizations to be prepared for various eventualities.
Suggested reads:
How to measure asset reliability with a bathtub curve?
A Quick Guide to Avoid Getting Pencil Whipped!
Benefits of planned maintenance
A good maintenance strategy is crucial for any property owner or manager. By investing in planned maintenance, you can:
- Minimize downtime — If a significant system breaks down, it can take days or weeks to fix. That’s the time when your property is not operating at full capacity. That total downtime could have been prevented or scheduled for a time that is less disruptive if you had been doing preventive maintenance.
- Increase your equipment’s lifespan — Preventing equipment failure extends the lifespan of your systems. For example, your property's HVAC systems, bathroom appliances, and other fixtures will last longer with proper care.
- Improve tenant satisfaction — When your tenants are happy, they’re more likely to renew their lease. And when they don’t have to deal with unexpected repairs, they’re even more comfortable. Nobody likes dealing with emergencies, especially in commercial properties with many tenants.
- Keep maintenance costs low — Emergency repairs in case of breakdowns are expensive. Urgency drives up the cost of labor and materials. If you can avoid those costs by avoiding emergency repairs, your bottom line will thank you.
You’re probably wondering how planned maintenance works. Here’s how.
How does planned maintenance work?
Here’s what the maintenance process looks like. A maintenance team consisting of certified professionals inspects the property. It then draws up a maintenance plan to fix any potential problems. The inspection includes tasks like:
- Cleaning and inspecting gutters and downspouts
- Inspecting the roof and making repairs as needed
- Checking for cracks or holes in the exterior of the building
- Servicing HVAC units
- Maintaining the landscaping
You can catch minor problems by performing them regularly before they become big. Keeping your properties in good condition avoids breakdowns and emergency repairs. And that can save you a lot of time, money, and headaches down the road.
Let’s say you have a rental property with 20 units. Each unit has its own HVAC system. You’re in the middle of summer, and one of the AC units breaks down. An emergency repair will cost you $500. But if you had been doing regular maintenance on the unit, it would have only cost you $200 to fix.
In this case, maintenance saves you $300.
But that’s not all. The repair cost also caused the unit to be out of service for two days. That’s two days where your tenants were uncomfortable. And it’s two days of lost rent — $200 per day, for a total of $400. So, in this case, scheduled maintenance saved you $700.
The best way to plan and execute maintenance is with the appropriate software.
Want to learn more?
Schedule a demo now and learn what Facilio can do for your business.
What is a planned maintenance system?
A planned maintenance system is a software solution that helps you with maintenance planning.
The software lets you create a database of your properties and each piece of equipment. You can then use this database to monitor how each piece of equipment performs.
The best software for the task is computerized maintenance management software (CMMS). A CMMS is a solution that helps you with all aspects of maintenance.
You can use a CMMS to track work orders, manage vendors, and energy, schedule preventive maintenance, and keep an inventory of spare parts and replacement parts.
With a CMMS, track and manage asset lifecycle to check if everything is working correctly, which makes it easy to spot equipment downtime.
You can also use the software to schedule these tasks. For example, you can set a task to inspect the HVAC system annually and assign contractors. Then, when the time comes, the software automatically generates a work order for the contractor.
Planned maintenance vs. unplanned maintenance
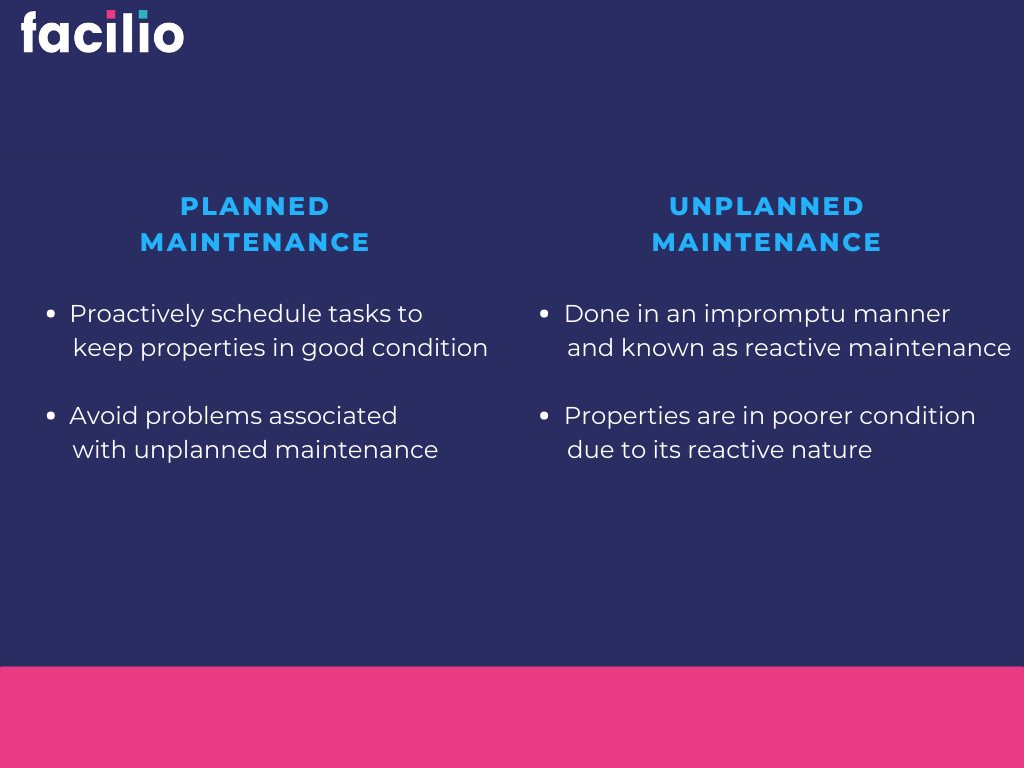
Unplanned maintenance is any repair that’s done on an as-needed basis. For example, if a pipe bursts, you’ll have to call a plumber to fix it. Unplanned maintenance is also known as reactive maintenance.
With unplanned maintenance, you’re constantly playing catch-up. You’re always reacting to emergencies and never have time to do preventive tasks. As a result, your properties are in poorer condition, and you end up paying more in the long run.
Planned maintenance is the opposite of unplanned maintenance. With planned maintenance, you proactively schedule tasks to keep your properties in good condition. By doing preventive tasks, you can avoid many problems that lead to unplanned maintenance.
Planned maintenance vs. preventive maintenance
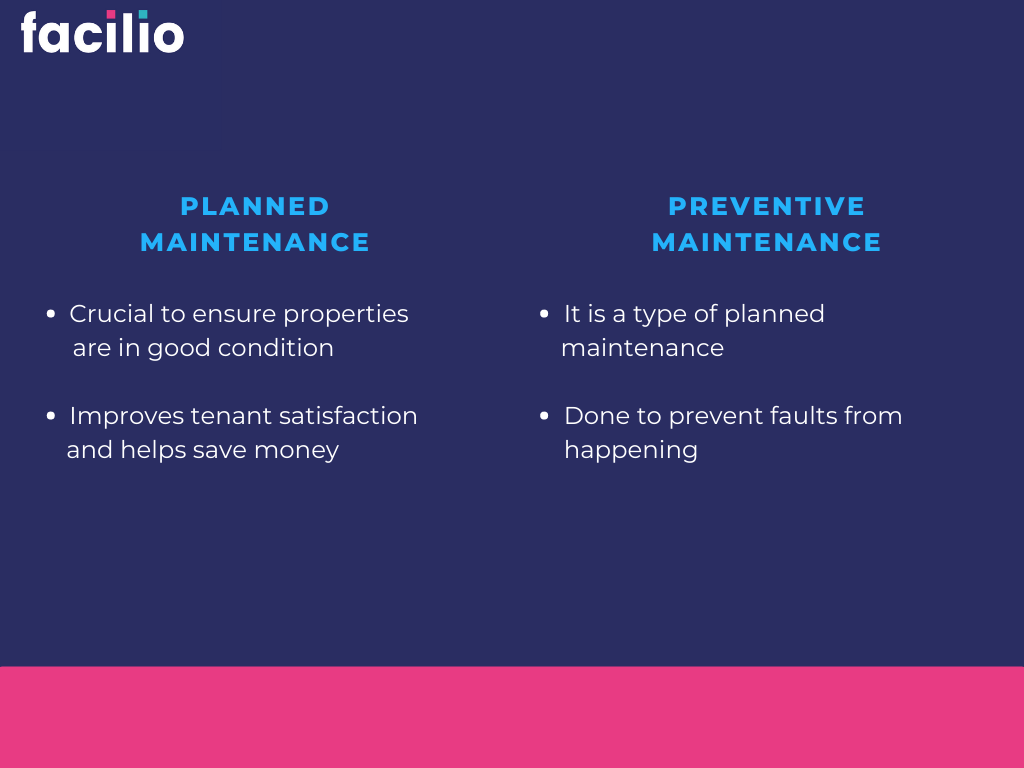
Preventive maintenance is a type of planned maintenance. But not all scheduled maintenance tasks are preventive.
Preventive tasks are those that are done to prevent something from happening. For example, an oil change in your car is a preventive task. You’re preventing the engine from wearing out prematurely.
While preventive maintenance is essential, it’s not the only planned task you should do. Both preventive and cosmetic tasks are crucial for keeping your properties in good condition.
Planned maintenance is a vital part of keeping your properties in good condition. It improves tenant satisfaction and saves you money in the long run.
The software can help you keep track of your properties and equipment, manage the maintenance planning process, and generate reports.
Suggested read: How to perform Facilities Condition Assessment?
Acing planned maintenance with Facilio
With Facilio, you can easily create a database of your properties and track each piece of equipment's key performance indicators (KPIs). It’s one of the best CMMS software that works as a centralized hub to simplify asset management. The software lets you generate work orders, schedule tasks, work prioritization, and increase asset lifespan.