Maintenance
Machine Maintenance: How Real-Time Data Helps Supercharge Asset Performance and Reduce Downtimes
What is machine maintenance?
Machine maintenance is checking, repairing, servicing, and replacing heavy-duty machinery parts or hand-operated equipment to ensure continued working order.
Machine maintenance is any equipment maintenance work that keeps mechanical assets in tip-top shape, a factory floor functional, and minimizes downtime.
Common machine maintenance activities like cleaning surfaces, lubricating gears, checking wear and tear, and monitoring equipment for potential signs of trouble, such as changes in energy consumption, vibrational patterns, or temperature.
Machine maintenance technicians perform these tasks during routine checkups, emergency maintenance, or planned maintenance.
Periodic machine assessment and machine control, sensor, and interface data help technicians evaluate whether to repair or replace machinery.
Check out this article and learn how office hoteling is changing the way we work!
Why is machine maintenance necessary?
Regular machine maintenance is crucial to detecting and repairing faults before they cause injury or death.
The right machine maintenance strategy aids you in predicting machine downtime, choosing the right corrective maintenance measures, and achieving maximum efficiency.
Continuous machine maintenance helps you:
- Improve asset lifespan throughout the asset lifecycle.
- Prevent complex, expensive repairs caused by negligence.
- Reduce unplanned downtime, which interrupts manufacturing.
- Minimize energy consumption and operating cost of systems.
- Keep equipment in working conditions and reduce fatalities or injuries.
Technicians combine different machine maintenance strategies and technologies, including cloud computing, the Internet of Things (IoT), and smart sensors, to complement scheduled visits and receive real-time maintenance alerts.
What are the types of machine maintenance?
A balanced maintenance program uses these eight machine maintenance strategies to keep assets functional and prevent worker injuries.
1. Reactive maintenance or breakdown maintenance is the maintenance you perform after an asset breaks down, faults, or malfunctions. Because of its unplanned and unexpected nature, reactive maintenance often results in emergency repairs.
2. Run-to-fail maintenance is similar to reactive maintenance but deliberately lets a machine run until it breaks down. However, you keep the labor and parts ready to get the machine up and running after it fails.
3. Preventive maintenance involves regular and routine asset maintenance. This type of maintenance helps you identify and repair problems before an asset fails. Preventive maintenance is of two kinds: time-based preventive maintenance (takes place at a regular time interval) and usage-based preventive maintenance (happens based on actual equipment usage).
4. Condition-based maintenance relies on internal sensors to gather asset performance data and decide whether maintenance is necessary to optimize performance. Real-time sensor readings help you better understand the chances of failure or performance issues.
5. Predictive maintenance uses data analysis to detect potential machine and equipment anomalies, failures, and defects. Real-time performance monitoring is key to correcting failures before they occur.
6. Prescriptive maintenance leverages artificial intelligence (AI) and machine learning to track real-time machine performance and automate maintenance work.
7. Routine maintenance includes basic maintenance activities, such as regularly checking, replacing, and regularly lubricating worn or damaged parts.
8. Corrective maintenance refers to technicians performing non-invasive maintenance tasks during routine inspection to get machinery back in working order.
Now that you know the types, let’s look at when to perform them.
Schedule a demo and learn why Facilio is the best option for your business.
How often should you perform different types of maintenance?
Ideally, you should perform machine maintenance at regular intervals per the machine operation and maintenance manual.
Also, consider creating a preventive maintenance schedule according to the recommended service interval, for example, the number of running hours or production cycle. Ongoing predictive maintenance activities like vibrational analysis or electrical monitoring are crucial to forecasting machine failure.
Examples of machine maintenance by industry
Industries that commonly use machine maintenance to maintain heavy equipment and avoid downtimes include:
- Plastic product manufacturers invest in maintaining plastic granulators, extrusion machines, injection molds, blow molding machines, vacuum forming equipment, and trim presses.
- Automotive manufacturers regularly maintain automated vehicle assembly equipment such as robotic welders, conveyor systems, shot pin cylinders, frame and toggle clamps, and pneumatic grippers.
- Food production units use machine maintenance schedules to protect cooking, storage, and packing tools like cookers, fryers, ovens, pumps, conveyor systems, and filling machines.
- Apparel production companies regularly repair and regularly service knitting, pressing, and sewing machines.
- Steel mills maintain heavy equipment such as electronic arc furnaces, lathes, reels, casters, and blast furnaces.
- Refineries perform machine maintenance on boilers, heat exchangers, furnaces, boilers, compressors, tanks, reactors, and pumps.
Schedule a call with us today and learn how you can seamlessly handle machine maintenance with a single platform.
Ways to improve machine maintenance
Improving machine performance is more straightforward with planning, precision, protection, and measurement.
- Planning ensures you have a strategy, parts, equipment, and labor to service and repair machines. The right plan prepares you to deal with planned maintenance tasks and emergencies.
- A precision maintenance strategy aids you in performing maintenance tasks accurately and consistently. Effective precision maintenance means your workers have the training, skills, tools, equipment, and maintenance materials, such as lubricants and spare parts, to follow the maintenance plan and complete tasks on time.
- Protection is all about keeping workers safe. Consider following the right lockout tagout (LOTO) procedure, inspecting electrical equipment, and conducting safety training at regular intervals.
- Asset performance measurement helps you create condition-based, prescriptive, and predictive maintenance plans based on real-time machine data. The more data, the better the performance.
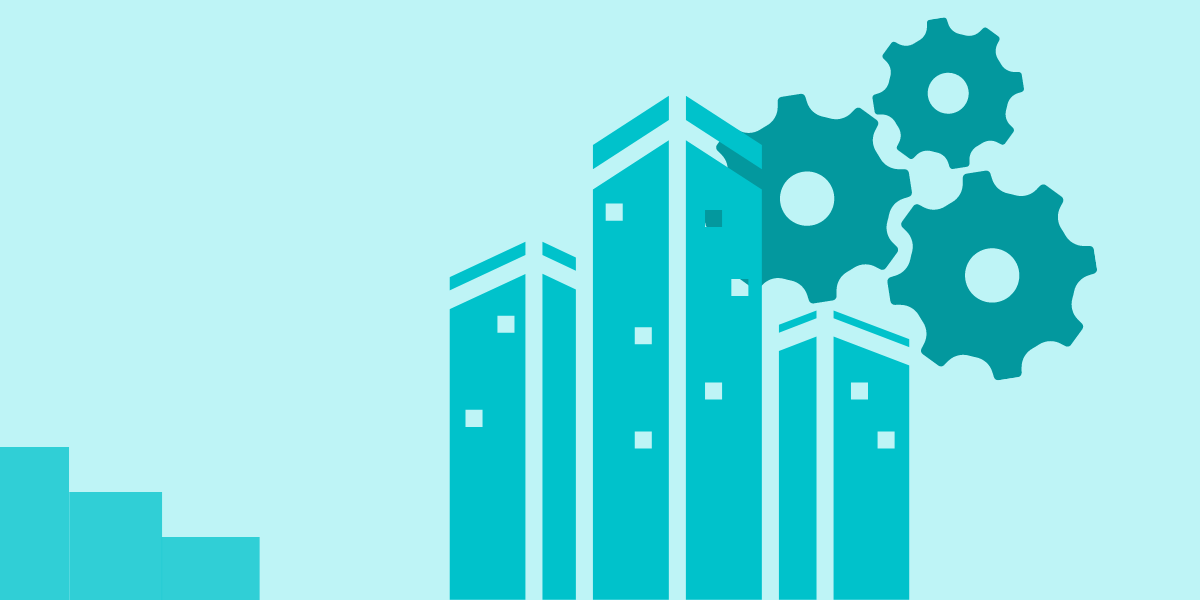
Machine maintenance with a CMMS
Machine maintenance is critical for optimizing the useful asset life of facility equipment.
With a computerized maintenance management system (CMMS), you can easily track maintenance operations and optimize physical equipment utilization across plants.
Want to optimize equipment maintenance at your facility? Schedule a demo to see how Facilio can help you streamline reporting, manage maintenance schedules, and optimize workflows.